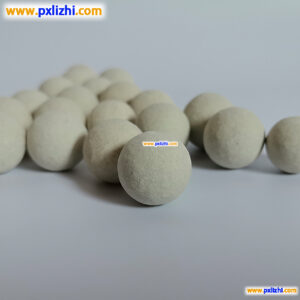
# Ceramic Ball Manufacturing Process and Applications
## Introduction to Ceramic Balls
Ceramic balls are highly specialized spherical components made from advanced ceramic materials. These precision-engineered spheres offer exceptional properties that make them valuable across numerous industries. The manufacturing process of ceramic balls requires strict quality control to ensure consistent performance in demanding applications.
## Raw Materials for Ceramic Balls
The production of ceramic balls begins with carefully selected raw materials:
– Alumina (Al2O3)
– Zirconia (ZrO2)
– Silicon nitride (Si3N4)
– Silicon carbide (SiC)
These materials are chosen based on the desired properties of the final product, such as hardness, wear resistance, or thermal stability.
## Manufacturing Process
Keyword: ceramic ball
### 1. Powder Preparation
The ceramic manufacturing process starts with high-purity ceramic powders. These powders are:
– Precisely measured
– Mixed with binders and additives
– Homogenized to ensure uniform composition
### 2. Forming Process
Several methods are used to form ceramic balls:
– Isostatic pressing: Applies uniform pressure from all directions
– Extrusion: Forces material through a die
– Injection molding: Suitable for complex shapes
### 3. Sintering
The formed balls undergo high-temperature sintering:
– Temperatures range from 1400°C to 1800°C
– Process duration varies from hours to days
– Results in dense, strong ceramic structure
### 4. Precision Grinding
After sintering, balls undergo precision grinding to achieve:
– Tight dimensional tolerances
– Superior surface finish
– Perfect sphericity
## Quality Control Measures
Stringent quality checks ensure ceramic balls meet specifications:
– Dimensional accuracy (±0.1 μm)
– Surface roughness (Ra < 0.01 μm)
– Hardness testing (up to 2000 HV)
– Roundness verification
## Applications of Ceramic Balls
### Industrial Bearings
Ceramic balls excel in bearing applications due to their:
– High hardness
– Corrosion resistance
– Light weight
– Electrical insulation properties
### Medical Devices
In the medical field, ceramic balls are used in:
– Joint replacements
– Dental implants
– Surgical instruments
### Aerospace Components
The aerospace industry utilizes ceramic balls for:
– Guidance systems
– Valve components
– High-temperature bearings
### Electronics Industry
Ceramic balls serve critical functions in electronics as:
– Insulators in high-voltage applications
– Substrates for microelectronics
– Components in sensors
## Advantages Over Metal Balls
Ceramic balls offer several benefits compared to their metal counterparts:
– Higher temperature resistance
– Better corrosion resistance
– Lower density
– Non-magnetic properties
– Longer service life
## Future Developments
Ongoing research focuses on:
– Nanostructured ceramic materials
– Improved fracture toughness
– Cost-effective manufacturing methods
– Hybrid ceramic-metal composites
## Conclusion
The manufacturing of ceramic balls combines advanced materials science with precision engineering to create components that outperform traditional materials in demanding applications. As technology advances, we can expect to see ceramic balls playing an even greater role across various industries.