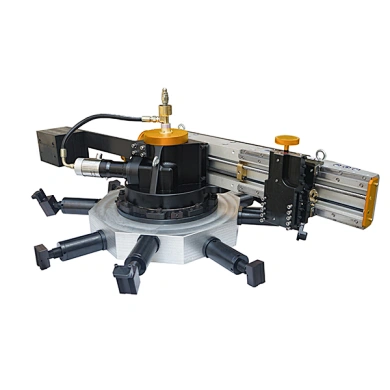
# On-site Flange Machining: Efficient Solutions for Industrial Maintenance
Keyword: On-site flange machining
## Introduction to On-site Flange Machining
In today’s fast-paced industrial environment, downtime can be incredibly costly. On-site flange machining has emerged as a game-changing solution for maintenance teams looking to minimize equipment downtime while ensuring precision repairs. This innovative approach brings specialized machining capabilities directly to the job site, eliminating the need for costly and time-consuming component removal and transportation.
## The Advantages of On-site Flange Machining
On-site flange machining offers numerous benefits that make it an attractive option for industrial maintenance:
– Reduced downtime: Equipment can often remain in place during machining
– Cost savings: Eliminates transportation and handling costs
– Precision work: Modern portable machines deliver factory-quality results
– Flexibility: Can be performed in challenging environments
– Safety: Minimizes risks associated with component removal
## Common Applications in Industrial Settings
This versatile technology finds applications across various industries:
### Power Generation
Critical for maintaining turbine flanges and heat exchanger components without prolonged shutdowns.
### Oil and Gas
Essential for pipeline flange repairs and offshore platform maintenance where removal isn’t practical.
### Chemical Processing
Enables precise machining of reactor vessel flanges and other critical components in corrosive environments.
### Manufacturing
Helps maintain production equipment with minimal disruption to operations.
## Key Technologies in Portable Flange Machining
Modern on-site flange machining relies on several advanced technologies:
– Portable milling machines with CNC capabilities
– Specialized facing equipment for flange surfaces
– Advanced measurement and alignment systems
– Custom fixturing solutions for various flange types
– Automated cutting tools for consistent results
## Best Practices for Successful On-site Machining
To achieve optimal results with on-site flange machining, consider these best practices:
– Conduct thorough pre-job inspections and measurements
– Ensure proper machine setup and alignment
– Use appropriate cutting tools and parameters
– Implement rigorous quality control measures
– Train personnel in both machining techniques and safety protocols
– Maintain equipment according to manufacturer specifications
## The Future of Field Machining Solutions
As industries continue to prioritize efficiency and cost-effectiveness, on-site flange machining is expected to evolve with:
– More advanced portable CNC systems
– Integration with digital twin technology
– Improved automation for consistent results
– Enhanced connectivity for real-time monitoring
– Development of specialized tools for unique applications
By adopting on-site flange machining solutions, industrial facilities can significantly improve their maintenance capabilities while reducing operational disruptions and costs. This approach represents a smart investment in long-term equipment reliability and productivity.