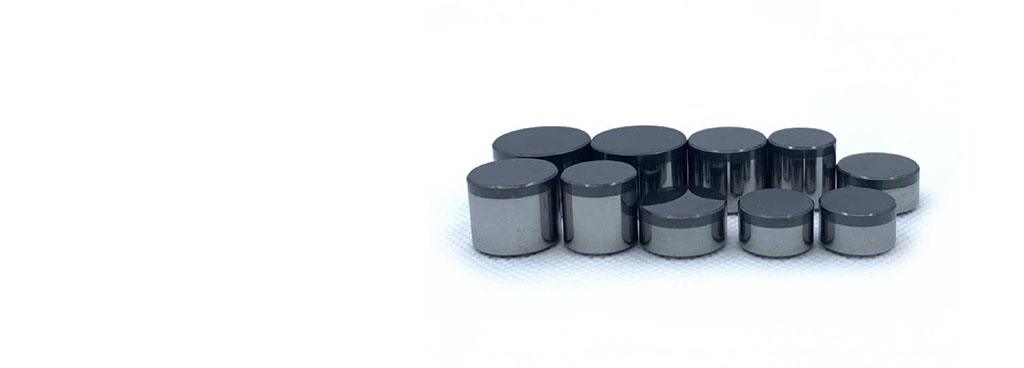
# OEM PDC Bit Cutter for Efficient Drilling Operations
## Introduction to PDC Bit Cutters
PDC (Polycrystalline Diamond Compact) bit cutters are essential components in modern drilling operations. These cutters are designed to provide superior performance, durability, and efficiency in various drilling applications. OEM PDC bit cutters are manufactured to meet specific industry standards, ensuring reliability and consistency in demanding environments.
## Benefits of Using OEM PDC Bit Cutters
Choosing OEM PDC bit cutters offers several advantages for drilling operations:
– Enhanced durability due to high-quality materials and manufacturing processes
– Improved drilling efficiency with optimized cutter designs
– Consistent performance across various rock formations
– Reduced downtime and maintenance costs
– Customizable options for specific drilling requirements
## Applications of PDC Bit Cutters
OEM PDC bit cutters are widely used in multiple drilling sectors:
### Oil and Gas Exploration
In the oil and gas industry, PDC cutters are crucial for efficient well drilling operations. They provide excellent penetration rates and longer service life compared to traditional cutter options.
### Mining Operations
Mining companies utilize PDC bit cutters for exploration and production drilling. Their ability to maintain sharp cutting edges in abrasive conditions makes them ideal for mineral extraction.
### Geothermal Drilling
The geothermal energy sector benefits from PDC cutters’ ability to handle high-temperature drilling environments while maintaining cutting efficiency.
## Key Features of High-Quality OEM PDC Bit Cutters
When selecting OEM PDC bit cutters, consider these important features:
– Diamond table thickness and quality
– Substrate material composition
– Cutter geometry and design
– Bonding technology between diamond and substrate
– Heat resistance capabilities
– Impact resistance ratings
## Maintenance and Care for PDC Bit Cutters
Proper maintenance extends the life of PDC bit cutters:
– Regular inspection for wear and damage
– Proper storage conditions to prevent degradation
– Correct handling procedures to avoid impact damage
– Appropriate cleaning after use
– Monitoring of drilling parameters to prevent excessive wear
Keyword: oem pdc bit cutter
## Choosing the Right OEM Supplier
Selecting a reliable OEM supplier for PDC bit cutters is critical for operational success. Consider these factors:
– Manufacturing expertise and experience
– Quality control processes
– Material sourcing and traceability
– Technical support and after-sales service
– Customization capabilities
– Industry certifications and compliance
## Future Trends in PDC Cutter Technology
The PDC cutter industry continues to evolve with new advancements:
– Development of more heat-resistant diamond composites
– Improved cutter geometries for specific formations
– Integration of sensor technology for performance monitoring
– Enhanced manufacturing techniques for greater consistency
– Environmentally friendly production processes
OEM PDC bit cutters represent a significant investment in drilling efficiency and performance. By understanding their benefits, applications, and maintenance requirements, operators can maximize their return on investment while achieving superior drilling results. Partnering with a reputable OEM supplier ensures access to high-quality cutters designed for optimal performance in challenging drilling conditions.