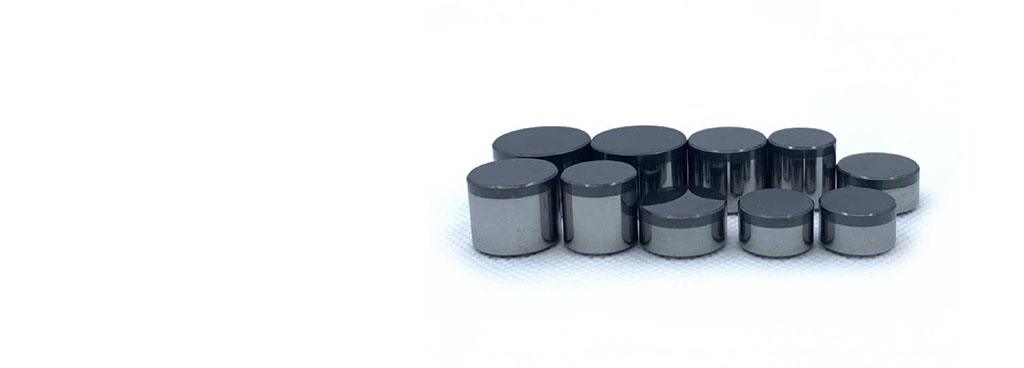
# PDC Cutter Supplier for Geological Exploration
## Introduction to PDC Cutters in Geological Exploration
Polycrystalline Diamond Compact (PDC) cutters have revolutionized the field of geological exploration. These advanced cutting tools offer superior performance in drilling operations, making them indispensable for modern exploration projects. As a leading PDC cutter supplier for geological exploration, we understand the critical role these components play in obtaining accurate geological data.
## Why Choose PDC Cutters for Exploration Drilling?
PDC cutters provide several advantages over traditional drilling tools:
– Exceptional hardness and wear resistance
– Improved rate of penetration (ROP)
– Longer service life compared to conventional bits
– Better stability in various geological formations
– Reduced drilling costs through increased efficiency
## Key Features of High-Quality PDC Cutters
When selecting a PDC cutter supplier for geological exploration, consider these essential characteristics:
### Diamond Layer Quality
The diamond table thickness and grain size significantly impact cutter performance. Our cutters feature optimally engineered diamond layers for maximum durability.
### Substrate Material
High-quality tungsten carbide substrates ensure proper support for the diamond layer and effective heat dissipation during operation.
### Interface Design
Advanced interface geometries between the diamond layer and substrate enhance impact resistance and thermal stability.
## Applications in Geological Exploration
PDC cutters are used in various exploration scenarios:
– Oil and gas exploration drilling
– Mineral exploration core drilling
– Geothermal energy exploration
– Scientific research drilling projects
– Water well drilling for hydrological studies
## Choosing the Right PDC Cutter Supplier
Selecting a reliable PDC cutter supplier for geological exploration requires careful consideration of several factors:
### Manufacturing Expertise
Look for suppliers with proven experience in PDC cutter production and a track record of supplying exploration projects.
### Quality Control Standards
Ensure the supplier maintains strict quality control measures throughout the manufacturing process.
### Technical Support
A good supplier should offer comprehensive technical support and cutter selection guidance for specific applications.
### Research and Development Capabilities
Choose a supplier that invests in continuous R&D to improve cutter performance and develop new solutions.
## Maintenance and Optimization Tips
To maximize the performance of your PDC cutters:
– Follow proper storage procedures to prevent damage
– Use appropriate drilling parameters for specific formations
– Implement regular inspection routines
– Consider cutter geometry optimization for challenging formations
– Monitor wear patterns to identify potential issues early
## Future Trends in PDC Cutter Technology
The PDC cutter industry continues to evolve with advancements in:
– Nano-structured diamond materials
– Improved thermal stability solutions
– Advanced cutter geometries
– Hybrid cutter designs
– Smart cutter technologies with embedded sensors
As exploration projects push into more challenging environments, the demand for high-performance PDC cutters will only increase. Partnering with an experienced PDC cutter supplier for geological exploration ensures access to the latest technologies and reliable cutting solutions for your drilling operations.