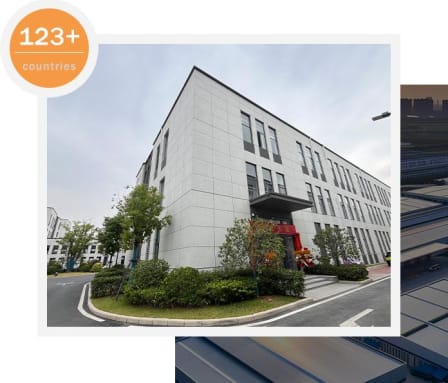
# PDC Bit Cutter Technology in Drilling Operations
Introduction to PDC Bit Cutters
Polycrystalline Diamond Compact (PDC) bit cutters, commonly referred to as PDC bit cutters, have revolutionized the drilling industry. These advanced cutting tools are designed to enhance drilling efficiency, reduce operational costs, and improve overall performance in various drilling applications.
How PDC Bit Cutters Work
PDC bit cutters consist of a layer of synthetic diamond particles bonded to a tungsten carbide substrate under high pressure and temperature. This unique combination provides exceptional hardness and wear resistance, making them ideal for cutting through hard and abrasive formations.
The cutting action occurs as the PDC cutter shears the rock formation rather than crushing it, which significantly reduces energy consumption and increases drilling speed.
Advantages of PDC Bit Cutters
- Superior Durability: PDC cutters last significantly longer than traditional roller cone bits in most formations
- Increased ROP: They typically achieve higher rates of penetration (ROP) compared to conventional bits
- Reduced Vibration: The shearing action creates smoother drilling with less vibration
- Cost Efficiency: Longer bit life translates to fewer bit changes and lower overall drilling costs
Applications in Drilling Operations
PDC bit cutters are widely used in various drilling operations including:
- Oil and gas exploration
- Geothermal drilling
- Mining operations
- Horizontal and directional drilling
- Water well drilling
Recent Technological Advancements
The PDC cutter technology has seen significant improvements in recent years:
- Enhanced thermal stability for high-temperature applications
- Improved impact resistance for harder formations
- Advanced cutter geometries for optimized performance
- Development of hybrid bits combining PDC and roller cone technologies
Choosing the Right PDC Bit Cutter
Selecting the appropriate PDC bit cutter depends on several factors:
- Formation characteristics (hardness, abrasiveness)
- Drilling parameters (weight on bit, rotation speed)
- Bit design and cutter placement
- Specific application requirements
Keyword: pdc bit cutter
Future of PDC Cutter Technology
As drilling operations push into more challenging environments, PDC cutter technology continues to evolve. Researchers are focusing on:
- Nanostructured diamond materials for enhanced performance
- Smart cutter technologies with embedded sensors
- Improved wear-resistant coatings
- Environmentally friendly manufacturing processes
The ongoing development of PDC bit cutter technology promises to further transform drilling operations, making them more efficient, cost-effective, and environmentally sustainable.