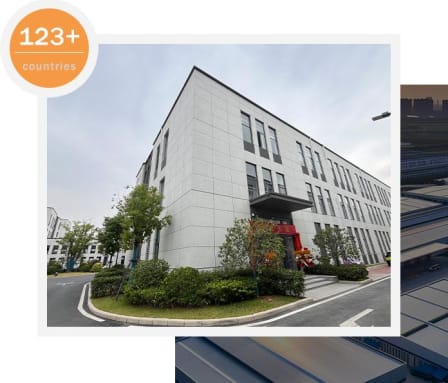
# PDC Bit Cutter: Essential Tool for Efficient Drilling Operations
PDC Bit Cutter: Essential Tool for Efficient Drilling Operations
When it comes to drilling operations, efficiency and durability are paramount. One of the most critical components in achieving these goals is the PDC (Polycrystalline Diamond Compact) bit cutter. This advanced cutting tool has revolutionized the drilling industry by offering superior performance in various challenging conditions.
What is a PDC Bit Cutter?
A PDC bit cutter is a cutting element made from synthetic diamond particles bonded together under high pressure and temperature. These cutters are then brazed onto the drill bit’s body, typically made of tungsten carbide. The result is an incredibly hard and wear-resistant cutting surface that can maintain its sharpness even under extreme conditions.
Key Advantages of PDC Bit Cutters
1. Exceptional Durability
Keyword: pdc bit cutter
PDC cutters are renowned for their outstanding wear resistance. The polycrystalline diamond layer can withstand abrasive formations much better than traditional tungsten carbide inserts, significantly extending the bit’s operational life.
2. Improved Rate of Penetration
The sharp cutting edges of PDC cutters allow for faster drilling speeds compared to conventional roller cone bits. This leads to reduced drilling time and lower operational costs.
3. Versatility in Formation Types
While particularly effective in soft to medium formations, modern PDC bit designs have expanded their applicability to harder formations as well, making them suitable for a wide range of drilling scenarios.
Applications of PDC Bit Cutters
PDC bit cutters are widely used in various drilling operations:
- Oil and gas exploration
- Geothermal drilling
- Mining operations
- Water well drilling
- Construction foundation drilling
Factors Affecting PDC Cutter Performance
Several factors influence the effectiveness of PDC bit cutters:
1. Cutter Quality
The manufacturing process and diamond quality significantly impact cutter performance. High-quality PDC cutters feature uniform diamond distribution and strong bonding to the substrate.
2. Bit Design
The arrangement of cutters on the bit face, along with the bit’s hydraulic design, affects overall drilling efficiency and cuttings removal.
3. Operational Parameters
Proper weight on bit and rotation speed must be maintained to optimize cutter performance and prevent premature wear or damage.
Maintenance and Care
To maximize the lifespan of PDC bit cutters:
- Inspect cutters regularly for signs of wear or damage
- Use appropriate drilling parameters for the formation being drilled
- Ensure proper bit cleaning between runs
- Store bits properly when not in use
The Future of PDC Technology
Continuous advancements in PDC cutter technology are pushing the boundaries of drilling performance. Innovations include:
- Improved thermal stability for high-temperature applications
- Enhanced impact resistance for harder formations
- Novel cutter geometries for specialized applications
- Advanced bonding techniques for increased durability
As drilling operations continue to push into more challenging environments, PDC bit cutters will remain at the forefront of drilling technology, offering the combination of speed, durability, and efficiency that modern operations demand.