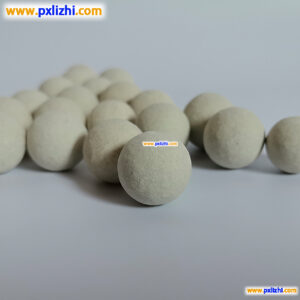
# Ceramic Ball Manufacturing Process and Applications
## Introduction to Ceramic Balls
Ceramic balls are precision-engineered spherical components made from various ceramic materials. These balls offer exceptional properties that make them suitable for a wide range of industrial applications. Their manufacturing process requires careful control to achieve the desired characteristics in terms of hardness, wear resistance, and dimensional accuracy.
## Manufacturing Process of Ceramic Balls
### 1. Raw Material Selection
The production of ceramic balls begins with the selection of appropriate raw materials. Common materials include:
– Alumina (Al2O3)
– Zirconia (ZrO2)
– Silicon nitride (Si3N4)
– Silicon carbide (SiC)
The choice of material depends on the intended application and required properties.
### 2. Powder Preparation
The selected ceramic powder is carefully prepared to ensure uniformity:
– Particle size distribution is controlled
– Additives may be included to improve sintering
– Powder is thoroughly mixed to achieve homogeneity
### 3. Forming Process
Several methods can be used to form ceramic balls:
– Isostatic pressing: Powder is compressed in a mold under high pressure
– Extrusion: Material is forced through a die to form spherical shapes
– Slip casting: Liquid ceramic slurry is poured into spherical molds
### 4. Green Machining
After forming, the “green” (unfired) ceramic balls undergo:
– Precision grinding to achieve spherical shape
– Size control to ensure dimensional accuracy
– Surface finishing to remove imperfections
### 5. Sintering
The formed balls are fired in high-temperature kilns:
– Temperatures typically range from 1400°C to 1800°C
– Process duration varies from several hours to days
– Controlled atmosphere may be required for certain materials
### 6. Final Processing
After sintering, the balls undergo final treatments:
– Precision grinding to achieve tight tolerances
– Lapping for ultra-smooth surfaces
– Quality inspection for dimensional accuracy and surface finish
Keyword: ceramic ball
## Applications of Ceramic Balls
### 1. Bearing Applications
Ceramic balls are widely used in bearing systems due to their:
– High hardness and wear resistance
– Corrosion resistance
– Lightweight properties
– Ability to operate in extreme temperatures
### 2. Valve Components
In valve applications, ceramic balls offer:
– Excellent chemical resistance
– Long service life
– Reduced maintenance requirements
– Improved sealing performance
### 3. Grinding Media
Ceramic balls serve as grinding media in various industries:
– Mineral processing
– Paint and pigment production
– Pharmaceutical manufacturing
– Food processing
### 4. Aerospace and Defense
Specialized applications include:
– Guidance systems
– Gyroscopes
– High-performance bearings for aircraft
– Military equipment components
### 5. Medical Applications
In the medical field, ceramic balls are used in:
– Joint replacements
– Dental implants
– Surgical instruments
– Diagnostic equipment
## Advantages of Ceramic Balls
Ceramic balls offer numerous benefits compared to metal alternatives:
– Higher hardness and wear resistance
– Lower density (reduced weight)
– Better corrosion resistance
– Higher temperature tolerance
– Electrical insulation properties
– Non-magnetic characteristics
## Quality Control in Ceramic Ball Production
Manufacturers implement strict quality control measures:
– Dimensional accuracy verification
– Surface finish inspection
– Material composition analysis
– Mechanical property testing
– Batch consistency monitoring
## Future Trends in Ceramic Ball Technology
The ceramic ball industry continues to evolve with:
– Development of new ceramic compositions
– Improved manufacturing techniques
– Nanotechnology applications
– Enhanced quality control methods
– Expansion into new application areas
As technology advances, ceramic balls are expected to play an increasingly important role in various high-performance applications across multiple industries.